Tunnel Kilns (隧道窑)
History
Tunnel kilns (隧道窑, Sui Dao Yao) are single-chamber continuous motion kilns, in which the wares to be fired are mechanically moved through a long “tunnel” from one end to the other. Tunnel kilns vary in size across ceramic types; in Yixing, most range from 50 to 100 meters in length. The movement is often near-imperceptibly slow, such that it takes more than ~12 hours for a ware to transit the kiln.
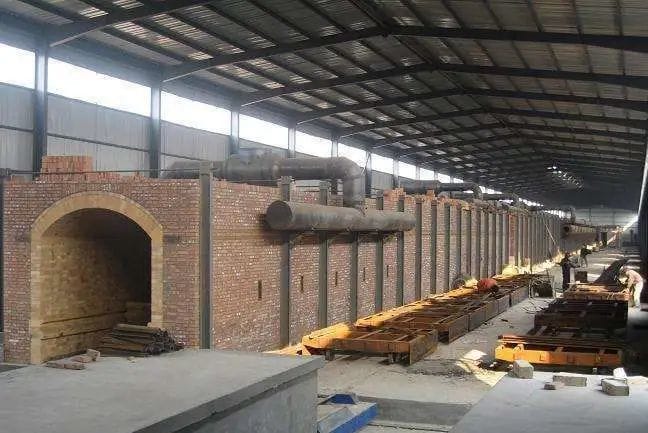
Yixing’s first tunnel kilns were built in 1965 CE[1], as part of the Communist government’s investments in the modernization and development of craft industries. Tunnel kilns are a suitable choice for industries with continuous mass production, firing a constant flow of wares per hour, which matched the goals for the government’s collectivization and investment. The tunnel kilns maintain a stable temperature and suffer little stress from sudden heating or cooling, greatly reducing the amount of maintenance required; while dragon kilns require repairs after every firing and downdraft kilns required regular maintenance at least annually, a tunnel kiln has an average 5 - 7 year maintenance window. This benefit comes at the cost of flexibility: a tunnel kiln is only suitable for mass production of wares with similar firing temperatures and firing times, with little room for modification available to either parameter; while F1 was able to successfully fire most zisha wares in a tunnel kiln, their use precluded them from firing a number of zisha ware types and style, including for example, zhuni clay and wuhui (焐灰) reduction fired wares[2]. Overall, the investment was eventually successful, and tunnel kilns remain in use today.
Tunnel kilns were increasingly mechanized over time, developing more efficient methods of progressing the ceramics through the kiln. Most contemporary tunnel kilns in Yixing are “Pushed Bat Kiln” (推板窑, Tui Ban Yao), a sub-type of tunnel kiln defined by the mechanism (the “bat”[3]) that moves the kiln-plate[4] through the kiln. In a pushed bat kiln, saggars are stacked on top of a ceramic kiln-plate; the mechanical “bat” pushes against the most recently added kiln-plate which is aligned side-by-side with the previous kiln plates, and the entire row of kiln-plates with saggars on top are pushed through the kiln[5], after the bat extends approximately 1 kiln-plate length, it retracts and a new kiln-plate is added to the sequence. While pushed bat kilns are generally smaller (~60m or less) than other types of tunnel kilns, there is little difference in the firing process or effect between the super-category of “tunnel kilns” and the various sub-categories. The increased machination of tunnel kilns reduced labor time and costs, as there is no manual loading of kilns in a batch process; instead, wares are stacked in saggars on top of kiln-plates, which are added at a constant rate.
This page is for paying subscribers only
Subscribe NowAlready have an account? Log in