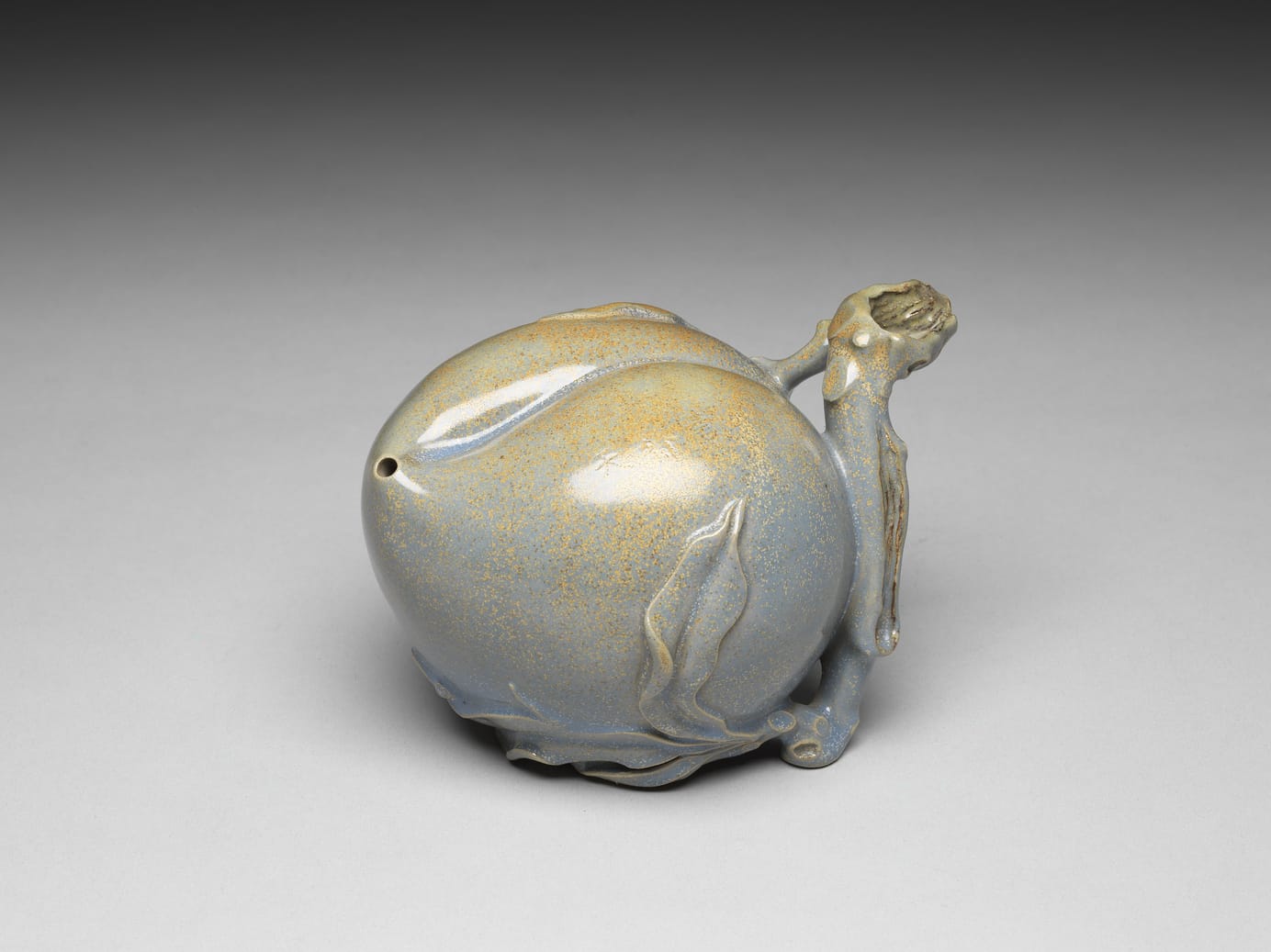
Editorial Conversation: Chapter 10, Section 9: An Overview of Yixing Kilns
The episode is also available on YouTube and Spotify.
A full transcript is included on the episode page and below:
[00:00:05] Jason Cohen: Hello everyone, I'm Jason Cohen, the author of An Introduction to the Art and Science of Chinese Tea Ceremony. Today we're discussing Book 2, Chapter 10, Section 1, Firing of Yixing Teapots, An Overview of Yixing Kilns. Here to talk about this chapter is our editorial team, Patrick Penny.
[00:00:21] Pat Penny: Hey, hey!
[00:00:22] Jason Cohen: Zongjun Li.
[00:00:23] Zongjun Li: Hello.
[00:00:24] Jason Cohen: And Emily Huang.
[00:00:25] Emily Huang: Da jia hao.
[00:00:27] Jason Cohen: Let's start with a quick round of definitions. What is a firing schedule?
[00:00:33] Pat Penny: So firing schedule is the planned time and temperature range that is going to occur within the kiln. So how long it's going to take for the kiln to get up to temperature, how long it's going to stay at a designated temperature, and then how long it's going to ramp down in temperature until it reaches ultimately a cooling phase.
[00:00:50] Jason Cohen: And that differs by different types of kilns, different types of ceramics.
[00:00:54] Pat Penny: Not only different types of kilns, but the target temperature is going to depend, like we see in Yixing here, on what ore predominantly your pot is firing. So there's different ranges that you want to hit depending on predominantly what ore is going to be in the kiln, or your kiln might hit a certain temperature, but you might stack your teapots in different arrangement depending on what temperature you want a certain strata to hit.
So the firing schedule is one thing, but there's even more technique that goes into it, which we'll discuss further.
[00:01:23] Jason Cohen: So it gets quite specific.
Zongjun, what is a kiln site and why are they an important concept when studying the development of kiln technology?
[00:01:31] Zongjun Li: Kiln changes all the time, like kiln types and kiln technology.
But the location of these kilns usually do not change a lot throughout history. So you can have Jian Yao (建窑). You can have Longquan Yao (龙泉窑). You can have Jingdezhen (景德镇). You can have Yixing (宜兴). All exist throughout hundreds of years of history in a similar location. So you are trying to study a heritage of how firing technology, ceramic technology exists and developed and evolved over time.
[00:02:04] Jason Cohen: Is there a reason why these kilns were consistently built in one area? Is there a geographic reason or a cultural reason? Or was it just easier once a kiln was built to keep building it there?
[00:02:15] Zongjun Li: Yeah. And also, kiln has a lifespan. You use the kiln. You fire the kiln. And over time, there can be a natural hazard. There can be war. Kiln collapse, and you need to rebuild them.
And once you have a site that's ongoing, you have groups of people, you have this ecosystem exist in the local community to support such industry. It's just easier for the kiln complex to exist in a similar location.
[00:02:44] Pat Penny: I'm just picking up a thread on that question too. I think a lot of these kiln sites were geographically defined by what materials that they had available to them or nearby to them. So when we think about Jingdezhen or primarily porcelain firing areas, there's probably a high amount of kaolin that was available in that area, which helped define that region as a kiln site. So I think that's definitely a part of it. Maybe there's a cultural piece to it as well, but probably the material was there and that helped then the culture rise around it.
[00:03:14] Zongjun Li: And also over time, the name of these locations become almost a brand, a label of a ware. Like Jingdezhen, like Longquan, like Yixing zisha, people will associate certain types of ceramic with a geographic location.
[00:03:30] Jason Cohen: Those are great points. Zongjun, picking up on something else that you said about these kilns. They get destroyed. There's natural hazards. You fire in them repeatedly and then they break down.
Is this a Ship of Theseus issue? Because Pat and I, when we were in South Korea, the kiln that we were firing our wares in was, I believe, 1600s. Jesuits built 1600s kilns.
But on the other hand, one of the times that we had visited, he had said that there had been some heavy rain and part of the kiln collapsed. And yet he just went back and with the same bricks, repaired it. Is that the same Kiln? Is that what it means as a kiln site?
Or are we talking about totally destroying a kiln and rebuilding something new on top of it, with new technology?
[00:04:09] Zongjun Li: I don't know. This is almost a question of Theseus' ship. If you keep manning a ship till the end, if it's still the same ship, I don't know. You can argue that it's the same ship. You can argue that it's a different ship.
[00:04:22] Jason Cohen: Unfortunately I mixed questions there.
I did both ask, is it the same kiln? But I also asked, is that always the case? So we're talking about repairs or are they actually destroying a kiln to replace it with something new from time to time?
[00:04:36] Zongjun Li: Yeah, I've visited a dragon kiln in Shunde. It's a kiln that was first built back in Ming Dynasty, and throughout times I believe the kiln has been rebuilt for at least three times?
So they do fixings to the kiln when it partially collapsed or sometimes it gets misfired and certain portion of the kiln gets overheated and then they need to mend it. But sometimes, in order to facilitate larger production, sometimes they need to reconstruct the firing chamber to extend the length of the kiln which requires basically a rebuild.
So I think such rebuild happened many times in different kilns throughout history for either increase the capacity or change certain feature of the kiln or sometimes firing a type of kiln to a different one might require a rebuild too.
[00:05:28] Jason Cohen: Emily, what is a saggar?
[00:05:31] Emily Huang: So a saggar, you can think of it as like a box where the artists would often put their partially done teapots or wares in the box and then put the entire box into the kiln to fire. And this is because they want to prevent any, could be dust or ash or any cracking that occurs in the kiln and scratching the surface or damaging the tea wares and teapots.
Yeah, it is often used to put in batches of saggars in a kiln.
[00:06:06] Jason Cohen: And not just dust or ash, but also that ash falling onto the ware and turning into glaze, getting a natural ash glaze.
[00:06:14] Emily Huang: Whether intentional or unintentional, most of the time we don't want that, hence the use of saggar.
[00:06:21] Jason Cohen: Why don't these boxes burn? What are they made out of?
[00:06:25] Emily Huang: They are made out of ceramics.
[00:06:28] Jason Cohen: They're fireproof clay boxes.
Moving away from definitions and into the discussion, how did kiln technology spread throughout China, and what role did the imperial government have in aiding this spread?
[00:06:39] Emily Huang: There has been a long tradition where not only just teawares, but even like calligraphies or poets where these artistic products would be sent into the Imperial Palace for the Emperor to, as a collection, to admire.
And this tradition produces a official kiln where for example, the one in Jingdezhen, it was an official kiln and they would commission and fire products that would be going into the Imperial Palace. They would also fire products for normal wares and for daily drinking and for collection. But the Imperial Palace helped with not only the reputation of the kiln, but also allowing it to having more opportunity to be improved, renovated, or expanded, etc.
And because different kilns are often located at different ore sites and with different clays, etc, there could be many, quote unquote, official kilns throughout China And so that tradition of sending it into the palace helped with the improvement of and development of the kiln and also of the entire industry.
[00:08:02] Pat Penny: Build off it a little bit. Certainly the imperial household not only commissioned wares, but were patrons for various arts, ceramic and otherwise. The literati do quite a similar function, maybe at a smaller scale individually, but as a whole, I think it's worth debate whether or not they had a larger impact on ceramic development versus the imperial family or not. That might be an interesting discussion to have at some point.
But outside of the space of commissions and patrons of art, going back probably quite far into the history of China, pre China as a country, but to the development of ceramic arts, a lot of these arts were just local forms of expression where you had tribes at the time who had materials on hand that they used either to form wares that were ceremonial in nature or eventually wares that were for daily use. And over time as these cultures come into contact with each other, trade probably took place and I think that's where a lot of the development of ceramics throughout Chinese history came from.
So you're having different groups who have different ores available to them, different firing technology, and different wares they focus on, and that is getting traded across China, by and large in part, probably pushed by imperial households or those who are rich and wealthy.
But I think it's really the trade that probably helped to foster development throughout China's history for ceramics.
[00:09:21] Zongjun Li: Yeah, the court really acts as a chief commissioner for all of the wares throughout China and also act as a aesthetic leader throughout time. So you can have a lot of these different aesthetic appreciation towards different types of ceramics in different dynasties, even different emperors within the dynasty. You can see the variations.
So usually we talk about the five most famous kiln in China. Ge Du Guan Ding Jun (哥汝官定钧 ). Guan is of course the official kiln, but they all have different specialties like the kiln change yao bian (窑变) in Jun Yao (钧窑). You can have the celadon in Ru Yao (汝窑). Those are all very interesting and very characteristic ceramics that gets appreciated in different eras of time.
And in those eras, you usually have the emperor or the court as the fashion leader to decide what is the imperial appreciation. What is our national ceramics?
So you can have for example, in Ming, there is a very heavy appreciation towards qinghua (清花) but into Qing dynasty, falangcai (珐琅彩) the very gaudy, colorful shape ceramic becomes the trend. So the court really acts as the key opinion leader at the time for ceramics.
[00:10:38] Jason Cohen: Falangcai has grown on me over time. I used to see it and think, oh, way too gaudy, but over time fen cai (粉彩), the rose famille verte has grown on me a bit.
[00:10:48] Zongjun Li: The pattern just reminds me too much of my grandma's pillow, you know.
[00:10:53] Jason Cohen: It's the opposite, it's the opposite. Your grandma's pillow is based on these beautiful motifs from earlier.
What were you saying, Pat?
[00:11:02] Pat Penny: I was just saying you've just become more gaudy over time. That's all there is to it.
[00:11:05] Jason Cohen: I have. There's even that footnote in book one. Someone will search for it, you'll find it.
One of the things that's worth talking about with the effect of the imperial family for the spread of technology, is that there were maybe two routes for primary spread.
There was, of course, the applied culture and learned technique of the craftsmen and kiln masters in each of these areas. They were often, at the villager level, illiterate. And then you have the mandarins working within the court system running the commissions and the imperial kilns for the empire, for the emperor.
And there were two methods of information spread between these different groups. There was the illiterate word of mouth, applied technique, applied knowledge, only some of which made it into either the gazetteers or made it into the manuscripts written by the literati, to promote their own expertise on these topics and to hopefully get a posting to run one of these major kiln sites or to become a negotiator or eventually later to become a respected collector whose wares and motifs and preferences would be encoded into the literati culture.
And so when we think about what did the Empire do to spread this technology? There were two things. One is they actually moved some of these illiterate kiln masters and artisans and craftsmen around. They would bring them to the Imperial Palace Workshop or to the Imperial Kiln from both within the province and from outside of the province, particularly Southern craftsmen going north into the imperial kilns or into the imperial palace workshop that would spread knowledge. And then they would purposely send them back, hoping to establish, particularly in the Qing dynasty, an imperial ideal of what these ceramics should be and that spread this applied knowledge at the same time that the literati were writing these other things.
So there was two sets of information exchanges, not all of which overlapped.
And that leads to an interesting question on how much of an impact other kiln sites had on the kilns of Yixing? Do we think of Jingdezhen having a major impact? Do we think of other kilns having a major impact? Can you name a kiln that had a major impact?
[00:13:22] Zongjun Li: Jun Yao (钧窑) certainly had a major impact to Yixing. You can find what they call Yijun (宜钧) nowadays. It's a very interesting imitation of Jun Yao aesthetic with Yixing material. Not necessarily have the same performance as regular Yixing zisha but certainly beautiful to look at.
[00:13:41] Pat Penny: Probably inspired by falangcai ( 珐琅彩), maybe some qinghua (清花) , we see overglazed enamel painted Yixing which certainly play off the motifs that we see from many other kilns.
[00:13:52] Jason Cohen: That was specifically started by the Imperial Palace Workshop. That's a great example.
What about Shiwan (石灣)? Shiwan at one point was a leading competitor to Yixing. Do we see any influence from Shiwan techniques?
Northern Guangdong kiln.
[00:14:09] Pat Penny: I remember reading about it in a previous chapter, but I'm not able to tie the two together.
[00:14:14] Jason Cohen: The short answer is yes.
What are some of the examples of unique kiln technology that may have been guarded by these independent businesses? Outside of the imperial kiln, you have the supplied knowledge, these kiln masters, what secrets are they keeping? What are they not telling the literati who are coming there to interview them and then write all about their techniques into manuscripts?
[00:14:35] Pat Penny: What are you not telling us? You just skipped right over the Shiwan with a yes. We want to hear it too.
[00:14:40] Jason Cohen: Someone's got to look this up. This is going to be a perfect comment for you on this chapter, Pat.
[00:14:45] Pat Penny: All right, I got a deep dive to do.
[00:14:47] Zongjun Li: Oh, the Shiwan looks like a Jun Yao too.
[00:14:51] Jason Cohen: Emily, that question to you. What are some examples of unique kiln technology,
[00:14:56] Pat Penny: heavily guarded technology question?
[00:14:58] Jason Cohen: Yes. What secrets are they keeping?
[00:15:01] Emily Huang: Secrets are called secrets because other people don't know about it.
[00:15:06] Pat Penny: I think this question has a secret answer, but if I had to guess, I would think probably glaze technology. So the mix of different colors, or the components that would go into a glaze, or at what temperature that glaze would vitrify. I'm sure things like that would be kept secret in certain areas.
The base clay material probably wouldn't be largely discussed with outsiders. It would be more expensive, but I'm sure that if you wanted to start a kiln to compete with another kiln, you could, if you in theory knew what the material composition was, import the organic material. I would think that probably the blend of material would be guarded.
I'm sure there's infrastructure technology right around the kiln itself, which there's some things you can see with the eye, but I'm sure that there's some specific design techniques that probably were not broadly shared beyond maybe what certain literati were writing or discussing. I imagine there was things they were probably told, hush, don't write too much about this.
[00:16:02] Jason Cohen: Yeah, that's a pretty good answer. So on the first one, glaze composition. Absolutely, that was often kept secret. On the second one, clay composition, that was much more difficult to keep secret because there was big mines and excavations going on.
And in fact, we did see someone start a competing kiln site for Yixing in the ROC, shipping tons of Yixing materials, tons of Yixing ore and processed clay to Shanghai for firing during the ROC in many of the export wares. So that actually did happen.
But the other one that was frequently kept secret is the firing schedule. Being able to determine the heat and the atmosphere in the kiln was a highly guarded secret.
Moving on, in this chapter, I argue for and use a linear developmental approach to the kiln technology for Yixing wares. Is this defensible? Why isn't a topological approach with sections on kiln design, fuel, atmosphere, and history a better structure for this chapter?
What do we gain by looking at this developmentally?
[00:17:00] Pat Penny: At least the way that I look at it, all of the newer innovations that come over time as the technology is developing build off of the initial technology. To go from modern and then go backwards or to take it section at a time, one section by section, you lose how a lot of these techniques build upon each other and the natural discovery that would have happened, leading to the progression of this technology over time. It's really a matter of one thing leading into the next, and so I think that linear progression makes sense.
[00:17:30] Zongjun Li: Yeah, and this progression really is a universal pattern in different kiln sites. A lot of these kiln locations undergo similar evolution throughout history. If you look at a lot of the natural development in different sites like Jingdezhen or Yixing, they all went through similar pattern of building, rebuilding, moving into modernization, and all the difficulties they are facing in modern era.
[00:17:59] Jason Cohen: What changed in the early 1600s in Imperial China that allowed for the founding of private kilns or the transition of some village kilns into private kilns?
[00:18:08] Pat Penny: There's economic reforms. So the Chinese economy, I think, started to move into more, I'm assuming, paper money. Although I could be wrong. Maybe it's coins.
[00:18:17] Jason Cohen: It was coinage.
[00:18:18] Pat Penny: Okay.
[00:18:20] Jason Cohen: And so what spurred that change? Early 1600s, Zongjun, why did China suddenly move from a barter system to a coin system?
Coins and paper money had existed previously before this. Why did it suddenly increase? Why did rural villagers go from predominantly bartering to a predominantly market economy?
[00:18:40] Zongjun Li: You see the paper system being developed and actually went to a perfection during Ming dynasty because you see the early signs of what they call the yin piao and yin hao. They're almost proto banks in China and spark of capitalism revolution, but got extinguished very sadly because the fall of the Ming empire.
So in the late 1600, we were seeing constant wars going on, civil war and also invasion from the North into the Middle Earth. And in such a turmoil era, the paper system will no longer sustain, you no longer have a stable government to endorse such system to exchange a certain amount of gold or silver with the paper in your hand. So people started to move into a coin system or other precious material system as the base of economy.
[00:19:35] Jason Cohen: This is all true for the merchant class. But what was going on with the farmers, the villagers? What was going on with the individuals who weren't merchants or mandarins, who didn't even have access to this type banking system?
The major reform in the Ming was that taxation moved from being payable in goods in kind to being payable in money, and all labor on behalf of the imperial government was now paid in coins. And so this injected massive amounts of coinage into China and gave coins to individuals who had previously had never been able to barter for them and had no reason to have them.
This demand was so great that it actually is part of what spread the Chinese empire only slightly legally into Southeast Asia with mines in Southeast Asia, Bhutan and elsewhere and also importing silver from South America, kick starting trade with Europe and partially opening up China to that trade.
And suddenly this availability of coinage spurs an entire new generation of individuals to begin producing goods for a new market economy, some of which was extinguished exactly as you said, some of which survived through the Ming and the ROC. But that early monetization is really what spurred privatization and the original idea that you can convert things that had been community property, village property, into private property, or construct things that competed with village property.
[00:21:03] Zongjun Li: A side anecdote from the overabundance of coin at the time, there were contemporary excavation of armor in North America that the local Indians or Native Americans were using Ming Dynasty coins to weave them together to build these armor for the warriors to wear.
That was quite amazing to see.
[00:21:24] Pat Penny: I've never heard that. That's pretty mind blowing.
[00:21:27] Jason Cohen: I hope that's the cover image for this episode.
Given that explanation, how did those exports then play a role? What were private kilns doing? They were producing for the domestic market, they were producing for the export market.
Did private kilns have an advantage in either of those spheres?
[00:21:45] Pat Penny: I would think private kilns would have an advantage for the export market. The reason I think that is your officially commissioned kilns from the imperial family, they're providing very specific things that they want and assumably in pretty high quantities. So I would think the official kilns probably have their hands decently full. And I would think the pay from the official kiln would be sustainable enough that they're not maybe going out and hunting for extra business.
Whereas these private kilns, it's probably easier for foreign entities to come in and commission with them. They don't have to compete with the imperial family or other high rank literati that might want wares from these official kilns. And I'm sure that the source of silver and other coinage for making export produced wares is probably pretty high.
So I think when we think about a lot of the wares that we've seen in museums that were export pieces. You do have many that are quite high quality and certainly came from official kilns but I've seen in a lot of museums in Southeast Asia, excellent collections that were obviously from private kilns, didn't bear a lot of the markings of some of these official kilns or the style. So I would think the private kilns thrived probably on the export market.
[00:22:55] Jason Cohen: That is all correct.
Given that, how did the quality of the private kilns compare to the quality of the imperial kilns?
[00:23:02] Pat Penny: It probably depends on which kiln you pick. I'm sure there's a range of quality, and we've all seen when we've gone to museums, a range of quality. There's pieces that are in those museums because they are museum grade pieces, and there's pieces that are there for educational purposes to show a variety of styles and contemporary availability of certain pieces.
It probably depends on who it was being exported for. So there's export pieces that are for royalty abroad of similar stature to the imperial family. And then there's also export pieces to it that are probably more for the merchant class or for the kind of everyday person working class and so I'm sure that the availability of exports from different private kilns reflects the different classes who this was being exported to.
[00:23:46] Zongjun Li: Yeah, even in some of the more famous private kiln clusters like Longquan, you can still see a very large variation of different qualities. You can have very top quality celadon and other types of ceramic, but still you can have this mass production kilns making daily usage wares for civilians. So the quality really varies depending on even which corner of the city you're visiting.
[00:24:11] Pat Penny: I think probably all of us own a cup that was a people's ware cup, right? And even between those cups, there's varying levels of quality.
[00:24:21] Jason Cohen: But don't all of us also own a Kangxi (康熙) imperial ware that vary in quality?
You can't see, but everyone is shaking their head no.
[00:24:30] Pat Penny: Everyone who signs up for Tea Technique, don't you send them a Kangxi commission piece?
[00:24:35] Jason Cohen: They get one Kangxi, that would be expensive, we'll send them a Guangxu (光緒).
So, I agree with everything that has been said. One of the other interesting points that I'll add to that is that the quality of the imperial kilns varied over time, both with the level of supply and what else was happening, what the government was spending money on. So there were in fact times where the official kilns, which were not imperial kilns or the private kilns, exceeded the quality of the imperial kilns. So much to the point that at various times the imperial kiln was shut down before being restarted at a later date.
Well, everyone, that's all the time that we have for today. Thank you for joining us in this edition of Tea Technique Editorial Conversations. Please join us again for our next conversation, Mature Firing of Zisha Clay.